Lean ความสูญเสีย 8 ประการ (8 Wastes DOWNTIME)
Lean ความสูญเปล่า (Wastes) 8 ประการ
แนวคิดแบบลีน (Lean Thinking) จะเน้นไปที่การสร้างคุณค่าที่ลูกค้าต้องการ (Value Added) โดยมุ่งลดหรือขจัดสิ่งที่ไม่สร้างคุณค่าให้กับลูกค้าให้หมดไปเรียกกระบวนการที่ไม่สร้างคุณค่าดังกล่าวว่า ความสูญเปล่า (Wastes) จากแนวคิดของ เจฟฟรีย์ ไลเคอร์ (Jeffrey Liker) ที่เขียนไว้ในหนังสือวิถีแห่งโตโยต้า (The Toyota way) ได้สรุปเรื่องราวความสูญเปล่าไว้ทั้งหมด 8 ประการ มีการนำมาเรียงลำดับคำต่อเนื่องไว้ว่า DOWNTIME เพื่อให้จำได้ง่ายและช่วยให้คิดว่ามันคือ เวลาที่เสียเปล่า ไม่ได้เกิดการสร้างคุณค่า ประกอบด้วย
Lean ความสูญเสีย 8 ประการ (8 Wastes DOWNTIME) การเพิ่มผลผลิต (Productivity Improvement) เน้นการลดความสูญเสียที่เกิดขึ้นจากการทำงาน โดยอาจการใช้แนวคิดการบริหารจัดการแบบลีน (Lean Management) เข้ามา ช่วยในการค้นหาความสูญเสียที่มี และหาวิธีในการลดความสูญเสียที่เกิดขึ้นในแต่ละขั้นตอนของการทำงาน ในแนวคิดการทำงานแบบโตโยต้า เราจะได้พบว่า "ความสูญเสีย 7 ประการ" ซึ่งในภายหลังได้มีการเพิ่มความสูญเสียไปอีกหนึ่งเป็น ความสูญเสีย 8 ประการ (8 Wastes) โดยบางครั้งเราอาจพบมีการจัดเรียงตามอักษรเรียกว่า DOWNTIME ความสูญเสียในงานที่พบได้แก่
Lean D ความสูญเสียจากการมีของเสียมากเกินไป (Defect lost) คือ งานที่ต้องแก้ไข (Defect) ผลิตสินค้าที่ไม่ได้คุณภาพ ทำให้ต้องมาเสียเวลาในการแก้ไข เสียทรัพยากรทั้งวัสดุ แรงงาน ตามมา การทำงานผิดพลาดเกิดงานเสียเกิดขึ้น ต้องมาทำซ้ำใหม่ (Rework) ก็เป็นค่าใช้จ่ายที่สูงมากสำหรับผู้ผลิต เนื่องจากของเสียเหล่านั้นอาจถูกเพิ่มคุณค่าให้กับตัวมันไปหลายขั้นตอนแล้ว แต่ไม่สามารถนำมาจำหน่ายได้ ทำให้เกิดความสูญเปล่า ของเสียจำนวนมากเกิดจากการตรวจสอบที่ผิดพลาดและละเลย ดังนั้นเมื่อการการผิดพลาดของกระบวนการใดๆก็ตาม ต้องรีบหาสาเหตุ (Problem Solving process) และแก้ไขให้เสร็จสิ้นโดยเร็วก่อนการผลิตใหม่จะเริ่มขึ้น และควรกระตุ้นให้พนักงานเข้ามามีส่วนร่วม
Lean O ความสูญเสียจากการผลิตที่มากเกินไป (Overproduction lost) เป็นความสูญเสียจากการผลิตมากเกินความต้องการ เกินกว่าความต้องการของลูกค้า ผู้ผลิตสินค้าต้องการผลิตสินค้าให้มีจำนวนมากพอที่จะขายให้กับลูกค้าได้และต้องไม่สูญเสียโอกาสในการขายสินค้าเมื่อลูกค้าต้องการ ดังนัั้นการผลิตสินค้าเก็บรอไว้จำนวนมากเป็นสาเหตุของการผลิตที่มากเกินไป เป็นการเพิ่มค่าใช้จ่ายในเรื่องการเก็บวัตถุดิบและสินค้าสำเร็จรูปในคลังสินค้า ระบบ JIT (just in time) จึงเป็นที่นิยมสำหรับการแก้ปัญหาดังกล่าวด้วยการผลิตให้พอดีกับความต้องการของลูกค้า
Lean W ความสูญเสียจากการรอคอยงาน (Waiting lost) การรอคอยจะเกิดขึ้นก็ต่อเมื่อวัตถุดิบไม่ถูกใช้ในกระบวนการผลิต และถูกเก็บไว้นานก่อนจะถูกนำมาใช้ต่อไป เนื่องมาจากกระบวนการก่อนหน้าหรือขั้นตอนก่อนหน้า ความเร็วในการทำงานไม่สอดคล้อง ความสูญเสียจากการรอมากเกินไปอาจเกิดเนื่องจากการไหลของวัตถุดิบในกระบวนการผลิตที่ไม่ดีพอ เกิดจากความไม่สมดุลย์ของความเร็วการผลิตหรือเกิดความล้าช้าเกินไปในการผลิต (over-long production) การรอคอยอาจจัดการได้ด้วยการปรับสมดุลย์ในด้านการผลิตให้มีความเร็วที่ใกล้เคียงกัน ทั้งด้านความสามารถของพนักงานในการผลิต การไหลวัตถุดิบที่ปราศจากอุปสรรค์ เวลาในการซ่อมเครื่องจักรที่รวดเร็วขึ้น และการเติมเต็มวัตถุดิบในคลังสินค้าได้อย่างพอดี การรอคอย (Waiting) โดยเฉพาะธุรกิจบริการจะเห็นได้ชัดเจน การรอคอยทำให้เกิดต้นทุนแฝงต่างๆ ตามมา
Lean N ความสูญเสียเนื่องจากไม่มีการใช้ความคิดจากทีมงาน (None use idea from team Lost) ไม่สามารถใช้บุคลากรที่มีความรู้ ความสามารถ ได้เต็มประสิทธิภาพ ความสูญเสียจากการไม่รับฟังความเห็นและข้อเสนอของคนในองค์กร มักเกิดจากการขาดความใส่ใจในการคัดเลือกคนงาน ใช้คนไม่ถูกกับงานและหน้าที่ หรือละเลยในเรื่องการฝึกอบรม พัฒนาแรงงาน รวมไปถึงการที่พนักงานเข้าและออกถี่เกินไปด้วย ทำให้องค์กรไม่ขยับปรับตัวไปไหน เพราะไม่ฟังเสียงของทีมงานของเราที่จะสร้างสรรค์องค์กรให้พัฒนาก้าวไปข้างหน้า
Lean T ความสูญเสียเนื่องจากการขนส่งเคลื่อนย้าย (Transportation lost) โดยไม่จำเป็น ความสูญเสียจากการขนย้ายมากเกินไป เป็นการเคลื่อนย้ายของวัตถุดิบทั้งก่อนและระหว่างกระบวนการที่มีระยะทางและเวลานานเกินไป อาจเกิดจากคลังสินค้าและโรงงานไม่ได้อยู่ใกล้กัน หรือแม้แต่ที่ตั้งของเครื่องจักรในกระบวนการผลิตที่อยู่ไกลกันมากเกินไป การจัดวางผังโรงงานที่ดี (Plant layout) เป็นหนทางหนึ่งที่ช่วยได้ จากการผลิตที่มากเกินไปมักจะเป็นผลให้เกิดการเก็บสินค้ามาเกินไปจึงต้องเสียเวลาในการขนย้ายหรือค้นหาสินค้ามากขึ้น
Lean I ความสูญเสียเนื่องจากการมีสินค้าคงคลังมากเกินไป (Inventory lost) มีการเก็บ Stock วัตถุดิบ หรือ Stock สินค้ามากเกินความจำเป็นความสูญเสียจากการมีวัสดุคงคลังมากเกินไป สินค้าคงคลังรวมถึง วัตถุดิบในการผลิต วัตถุดิบระหว่างการผลิต และสินค้าสำเร็จรูป ไม่ควรมีมากเกินไป การมีวัตถุดิบที่ไม่ได้ใช้ในกระบวนการเก็บอยู่ ทำให้พื้นที่การทำงานลดลง โดยไม่เกิดคุณค่าขึ้นโดยเฉพาะวัตถุดิบระหว่างการผลิต (Work in process) ดังนั้นผู้ผลิตจึงควรวางแผนการผลิตและพยากรณ์การผลิตให้ดี โดยร่วมมือกับลูกค้าและคู่ค้า และการใช้เทคนิค Kanban มาช่วยเพื่อดึงวัตถุดิบมาผลิตอย่างพอดีตามความต้องการ
Lean M ความสูญเสียจากการเคลีอนไหวมากเกินไป (Motion lost) เป็นการเคลื่อนไหวที่ไม่จำเป็นในการทำงาน ซึ่งส่งผลทำให้ความสามารถในการทำงานมีค่าต่ำกว่าที่ควรจะเป็น ความสูญเสียจากการการเคลื่อนที่มากเกินไปเช่น การเคลื่อนย้ายสิ่งของโดยไม่ใช้เครื่องมือที่เหมาะสมช่วย และการทำงานที่ขาดมาตรฐานการทำงาน ทำให้เกิดการเคลื่อนไหวที่ไม่เหมือนกันตลอดระยะเวลาการผลิต ซึ่งจะส่งผลให้คุณภาพของชิ้นงานไม่สม่ำเสมอ เกิดของเสียจำนวนมาก และใช้เวลาในการทำงานมากและไม่เท่ากันในแต่ละครั้งของการผลิต การใช้ Value Stream Mapping และ 5 ส จะช่วยลดสิ่งเหล่านี้ได้ การเดิน เอื้อม หัน ซ้าย-ขวา หน้า-หลัง เสียเวลาในการทำงานทั้งนั้น ต้องหาวิธีการทำงานที่สะดวก รวดเร็ว ที่จะเคลื่อนไหวให้น้อยที่สุด
Lean E ความสูญเสียจากการมีกระบวนการมากเกินไป (Extra Processing) เป็นความสูญเสียจากการมีขั้นตอนการทำงานมากเกินความจำเป็น การมีกระบวนการมากเกินความจำเป็นอาจหลีกเลี่ยงได้ เช่น การจัดกระบวนการใหม่ให้อยู่ใกล้กันมากขึ้นจนเป็นกระบวนการเดียวกัน (Manufacturing cell) เพื่อประโยชน์ในการใช้เครื่องมือร่วมกัน และสามารถช่วยเหลือกันได้เมื่อต้องการ หรือการใช้เครื่องมือที่เหมาะสมกับการทำงานแทนการทำงานที่ไม่ถูกวิธี สามารถแก้ไขโดยใช้สายธารแห่งคุณค่า (Value Stream Mapping) มาช่วยลดกิจกรรมที่ไม่ก่อให้เกิดคุณค่าขึ้นในโรงงานได้ ขั้นตอนต่างๆ ไม่เคยมีการปรับปรุงเปลี่ยนแปลง มาตรฐานทำมาอย่างไรก็เก็บไว้แบบนั้นไม่มีการศึกษาพัฒนาขั้นตอนการทำงานอย่างจริงจัง หรือไม่ได้ค้นหาเทคโนโลยีเข้ามาช่วยให้ทำงานได้ง่ายยิ่ง
ไทอิจิ โอโน (Taiichi Ohno) อดีตผู้อำนวยการผลิตของโตโยต้า กล่าวไว้ว่า “การพิจารณาช่วงเวลาตั้งแต่ที่ลูกค้าสั่งซื้อจนถึงเมื่อรับเงินจากลูกค้า เป็นเรื่องที่จะต้องลดช่วงเวลานั้นให้สั้นลงมากที่สุด ซึ่งจะเกิดได้เมื่อเราดำเนินการกำจัดความสูญเปล่าหรือสิ่งที่ไม่เกิดประโยชน์ต่อลูกค้า” ซึ่งปัจจุบันแนวคิดลีนจะทำให้การผลิตมีประสิทธิภาพสามารถที่จะแข่งขันในตลาดได้ยืนยาว
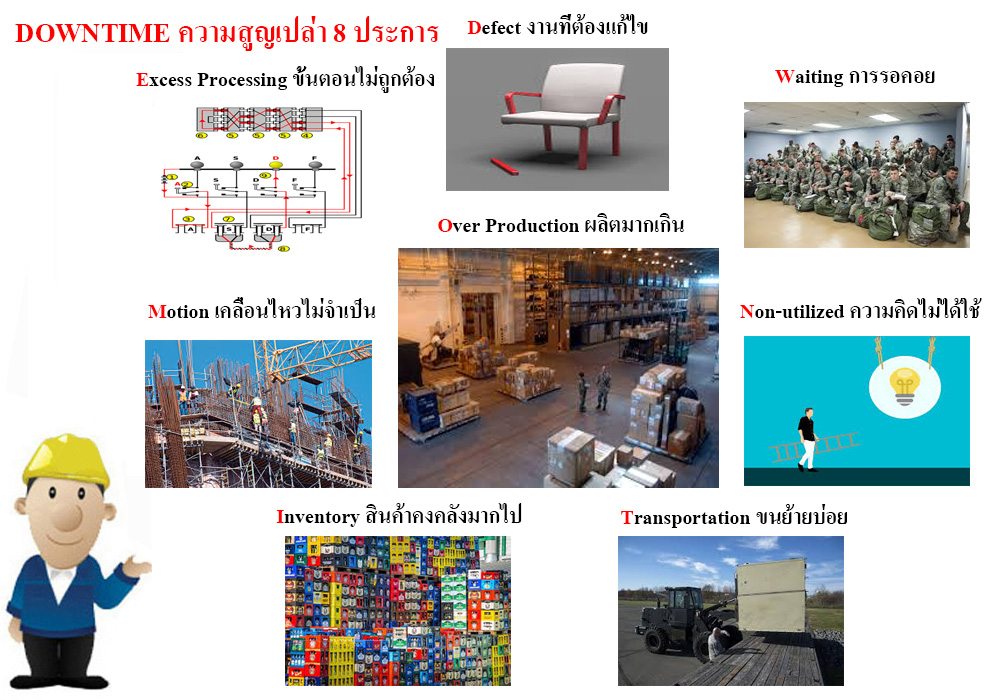
------------------------------------------------
ที่มาข้อมูล
ภาพและรวบรวมโดย www.iok2u.com